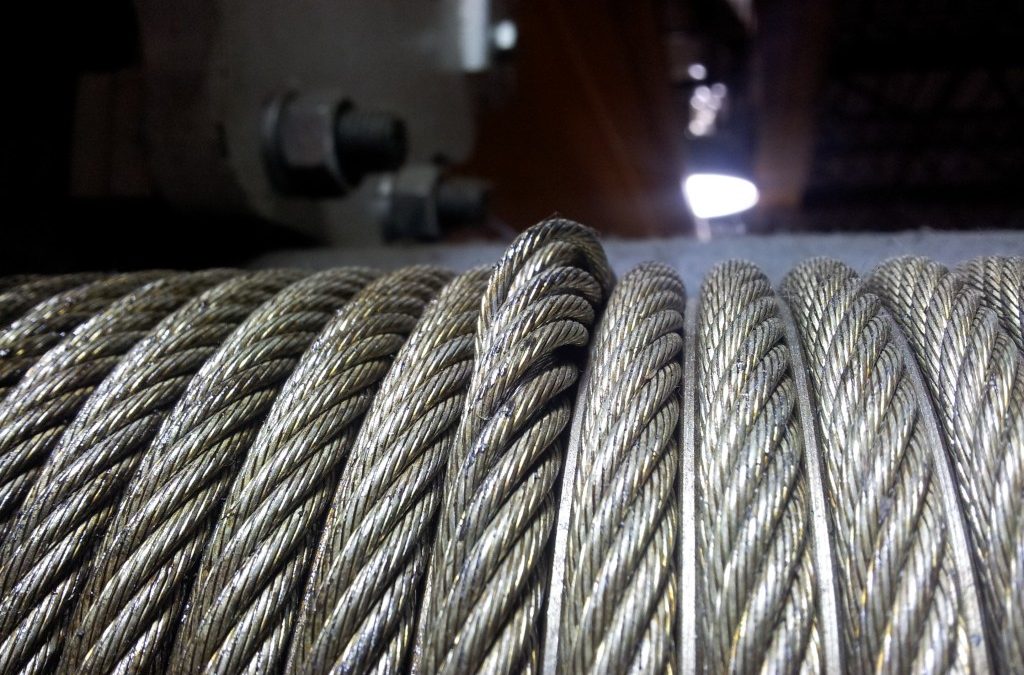
Heavy machineries and equipment need supervision on regular intervals and if need be; the parts need to change too as they start to wear off. If not attended properly, one may experience downtime more often than not. Even if a single part of the whole setup needs to get replaced in the machinery, it should be replaced in the due time.
With wire rope slings, it is imperative to check the hoist & the wires ropes both to maintain their health along with the productivity of the machinery. But wear and tear happen and you cannot control or reverse the damage; you can just monitor it and have it replaced after the wire rope has run its life.
You should & must remove & retract the wire rope sling from service with immediate effect; if the following conditions are in play:
1. WIRE BROKEN
Broken wires can really put a lot of load on the other wires which are still connected and the sling won’t be able to handle the same load with less number of wires or weakened wires due to sudden load shift; if at all, they are not broken.
2. METAL LOSS
Metal loss is a kind of wear & tear which is the first sign to look for if you think the wires should be changed. Wearing off or scraping off, of 1/3 the original diameter of the outside individual wires is called metal loss. Metal wires ropes, which when experiencing friction due to continuous usage have this symptom which makes them weaker, with every use.
3. DISTORTION
Wire ropes which are experiencing kinking, crushing will lose their tensile strength overtime due to overuse & misuse. Distortion damages the wire ropes a great deal because they get bent, crushed kinked out of their original shape which shrinks their life in every sense.
4. HEAT DAMAGE
Heat doesn’t cause metal a lot of damage but it sure causes a lot of damage to the lubricants which keeps the wire rope healthier for a longer period of time. Any kind of metallic discoloration or loss of internal lubricant caused by heat exposure can bring a long downtime for you.
5. DAMAGED END ATTACHMENTS
End attachment cracked, bent due to load push/pull or broken fittings due to mishandling can make can also cause operations to completely stop for a while and you will lose production time, value and it will cost you a lot in every way. Also, any evidence that eye splices have slipped, or tucked strands have moved will cause a major machinery damage if not attended to in time.
These are the 5 major reasons why you should change the wire rope hoists before they put you and your operations into great trouble. The supervisor and the operator can handle this if they are properly trained and have some experience with the same. A regular check by the operations head will also add another layer of protection on to it.